1.2311 Plastic Mold Steel
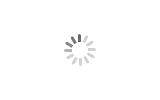
Prehardened plastic mould steel with good machinability, better than steel grade Mat. No. 1.2312, suitable for texturing.
Properties:
● International universal plastic die steel, vacuum degassing and ESR remelting, sulfur content and gas content is very low, mirror polishing performance is excellent, after forging and rolling processing and ultrasonic testing without cracks, pre-hard state delivery, no need for reheat treatment can be directly processed to the finished product, shorten the construction period;
Applications:
● Suitable for thermoplastic plastic injection mold, extrusion mold, blow mold, suitable for large and medium size and precision plastic mold molding parts, home appliance appearance mold, etc.
Parameters
Grade | Chemical Composition (%) | |||||||||
C | Si | Mn | Cr | Mo | P | S | ||||
GB | 3Cr2Mo | 0.28~0.40 | 0.20~0.80 | 0.60~1.00 | 1.40~2.00 | 0.30~0.55 | ≦0.03 | ≦0.03 | ||
ASTM | P20 | 0.28~0.40 | 0.20~0.80 | 0.60~0.00 | 1.40~2.00 | 0.30~0.55 | ≦0.03 | ≦0.03 | ||
DIN | 1.2311 | 0.35~0.45 | 0.20~0.40 | 1.30~1.60 | 1.80~2.10 | 0.15~0.25 | ≦0.03 | ≦0.03 | ||
ISO | 618 | 0.28~0.40 | 0.20~0.80 | 0.60~1.00 | 1.40~2.00 | 0.30~0.55 | ≦0.03 | ≦0.03 | ||
Specification | Round Bar Ø (mm) | Flat Bar (mm) | ||||||||
Hot Rolled | Hot Forged | EAF | ESR | |||||||
Ø12~Ø50 | EAF | ESR | Thickness | 20~200 | 20~450 | |||||
Ø50~Ø250 | Ø50~Ø650 | width | 105~610 | 610max |
Physical properties (average values) at ambient temperature
Modulus of elasticity [103 x N/mm2]: 210
Density [g/cm3]: 7.83
Thermal conductivity [W/m.K]: 34.0 (100oC), 34.0 (150oC), 33.6 (200oC), 32.9 (250oC), 31.9 (300oC), in quenched and tempered condition.
Soft Annealing
Heat to 710-740oC, cool slowly in furnace. This will produce a maximum Brinell hardness of 230.
Stress Relieving
Stress relieving to remove machining stresses should be carried out by heating to approx. 650oC, holding for 1-2 hours at heat, followed by air cooling. This operation is performed to reduce distortion during heat treatment.
Hardening
Harden from a temperature of 830-880oC followed by oil or air quenching or warm bath quenching 180-220oC. Hardness after quenching is 51 HRC.
Tempering Temperature (oC) vs. Hardness (HRC)
100oC | 200oC | 300oC | 400oC | 500oC | 600oC | 700oC |
51 | 50 | 48 | 46 | 42 | 36 | 28 |
Forging
Hot forming temperature: 1050-850oC.
Corrosion Resistance
This is a steel alloy and it will corrode or rust unless protected.
Welding
This alloy is weldable by conventional methods.
Cold working
This steel may be readily cold worked by conventional tooling with the alloy in the annealed condition.