1.2343 Hot Work Tool Steel
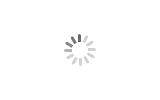
H11 is one of the Hot Work, Chromium type tool steels. It is relatively low in carbon content and has good toughness and deep hardens by air quench from heat treatment. Good combination of toughness, hardness and wear resistance in hot. Resistance to softening and to cracking.
Properties:
● The air-cooled hardened steel has good toughness, good thermal strength, thermal fatigue performance and certain wear resistance under medium temperature operation.
Applications:
● Suitable for hot punch, casting die, forging die, hot shear blade, extrusion die.
Parameters
Grade | Chemical Composition (%) | |||||||||
C | Si | Mn | Cr | Mo | V | P | S | |||
GB | 4Cr5MoSiV | 0.33~0.43 | 0.80~1.20 | 0.20~0.50 | 4.75~5.50 | 1.10~1.60 | 0.30~0.60 | ≦0.03 | ≦0.03 | |
ASTM | H11 | 0.33~0.43 | 0.80~1.20 | 0.20~0.50 | 4.75~5.50 | 1.10~1.60 | 0.30~0.60 | ≦0.03 | ≦0.03 | |
DIN | 1.2343 | 0.33~0.41 | 0.80~1.20 | 0.25~0.50 | 4.80~5.50 | 1.10~1.50 | 0.30~0.50 | ≦0.03 | ≦0.02 | |
JIS | SKD6 | 0.32~0.42 | 0.80~1.20 | ≦0.50 | 4.50~5.50 | 1.00~1.50 | 0.30~0.50 | ≦0.03 | ≦0.02 | |
Specification | Round BarØ (mm) | Flat Bar (mm) | ||||||||
Hot Rolled | Hot Forged | EAF | ESR | |||||||
Ø12~Ø50 | EAF | ESR | Thickness | 20~200 | 20~450 | |||||
Ø50~Ø250 | Ø50~Ø650 | width | 80~610 | 610max |
Physical properties (average values) at ambient temperature
Modulus of elasticity [103 x N/mm2]: 215, 176 (at 500oC), 165 (at 600oC)
Density [g/cm3]: 7.80, 7.64 (at 500oC), 7.60 (at 600oC)
Thermal conductivity [W/m.K]: 25, 28.5 (at 500oC), 29.3 (at 600oC)
Electric resistivity [Ohm mm2/m]: 0.52, 0.86 (at 500oC), 0.96 (at 600oC)
Specific heat capacity[J/g.K]: 0.46, 0.55 (at 500oC), 0.59 (at 600oC)
Coefficient of Linear Thermal Expansion 10-6 oC-1
20-100oC | 20-200oC | 20-300oC | 20-400oC | 20-500oC | 20-600oC | 20-700oC | 20-700oC |
9.8 | 12.5 | 13.0 | 13.2 | 13.5 | 13.7 | 13.8 | 14.0 |
Soft Annealing
Heat to 800-840oC, cool slowly in furnace. This will produce a maximum Brinell hardness of 229.
Stress Relieving
Stress relieving to remove machining stresses should be carried out by heating to 650oC, holding for one hour at heat, followed by air cooling. This operation is performed to reduce distortion during heat treatment.
Hardening
Harden from a temperature of 1000-1040oC followed by air, oil quenching or warm bath quenching 500-550oC. Hardness after quenching is 50-56 HRC.
Tempering Temperature (oC) vs. Hardness (HRC)
100oC | 200oC | 300oC | 400oC | 500oC | 550oC | 600oC | 650oC | 700oC |
53 | 52 | 52 | 52 | 54 | 52 | 48 | 38 | 30 |
1845 | 1790 | 1790 | 1790 | 1910 | 1790 | 1570 | 1200 | 970 |